Why is detecting “Core Pin Breakage” critical to avoid serious accidents? How to implement it in HPDC.
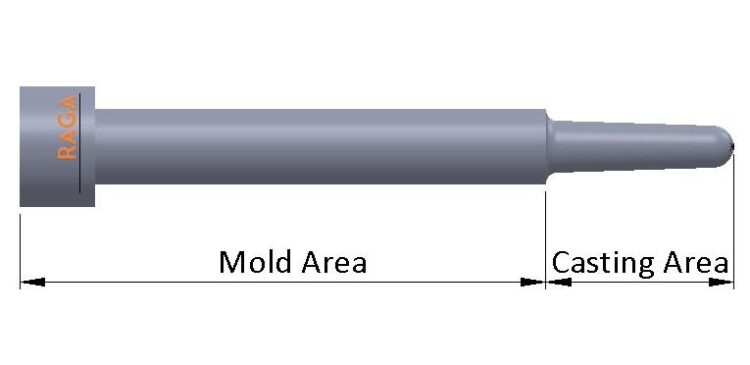
Core pins
Core pins also called as hole forming pins are an important part of the mold. They are used to create holes in the casting post solidification of molten aluminum.
Core pin is divided into two primary parts:
- Mold area: This remains inside the mold for guiding it to be in the right location
- Casting area: This remains inside the cavity for forming hole
Why do core pins break?
One that remains in the Casting area is slender in diameter and long. It is exposed to molten aluminum at 700 °C. This area is exposed to very high thermal & mechanical stresses, making it prone to wear and shear. Core pin wear can be taken care of by replacement or polishing. But core pin breakage has to be immediately replaced.
The problem arises for core pins which have slender holes for jet cooling right upto the edge of the pin. During solidification it runs highly pressurised water inside to enable faster heat transfer. The pin undergoes severe thermal stresses as compared to solid ones. And due to thin wall thickness, it has high chances of failure at the weakest area.
Jet cooled core pins fail owing to the following reasons:
- More drift in jet cooling hole of core pin
- Improper draft in the casting area
- Improper design of cooling hole
- Improper manufacturing quality
- Blockage inside the pin
- Exposed to thick mass of aluminum like in gate area
The breakage occur at three stages:
- During the solidification
- During the opening of Mold
- During the ejection of casting
Impact of core pin breakage
An Italian Association of chemical engineering report in 2019, based on a serious accident happening in Norway mentioned:
“Water trapped in molten aluminium (660 ˚C) can expand 4400 times. The explosion energy of 10 kg TNT roughly corresponds to the explosion energy of 1 kg hydrocarbon. Explosion due to water in molten metal is a well-known hazard in the metal melting industry, and it is critical to prevent water from entering the molten metal.”
In the event of breakage of the core pin, highly pressurised water can splurge into molten aluminum undergoing solidification. In one such accident in a die casting plant in the USA, it had serious loss of life and assets.
Methods to avoid it
Die casters around the world are realising the potential of this hazard and putting in place processes and methods to minimise this occurrence or even avoid it fully.
Some of the methods used are:
- Ensure that you use jet cooling core pin hole drift angle after conducting a 100% check.
- Replacement of jet cooled core pins before their breakage history
- Inspection of pins at frequent intervals for any visible development of surface cracks
- Die maintenance in case of any water leakage in the jet cooling circuit
Above methods depend on the skill of the operator and are man dependent.
Every die caster using jet cooling should consider methods of fool proofing (Poka Yoke) and make detection of breakage as part of the jet cooling process. The breakage could be detected
- Before the start of shot
- During the pin breakage and water leakage starts
Option 1: Detecting pin breakage in individual system/circuit of jet cooling
In this method a PBDD (Pin Breakage Detection Device) is used to detect breakage of core pin. In this device A separate air or water cycle is run after every die casting cycle. The drop in pressure would indicate leakage or breakage in the line.
As there is a breakage detected by the machine, it generates an alarm and even stops the die casting machine.
This could be done by equipping/modifying the jet cooling machine & mold with a pin breakage detection system (PBDD). This works on individual systems/circuits (2 or 4 or 6 Depending on number of circuits in the machine)
Option 2: Detecting pin breakage in particular pins
For detection pin breakage for particular pin need to use Flow sensing device (FSD). This senses water flow during the cycle and generates an alarm for any deviation. Low water flow indicates breakage or blockage or leakage of the pins.
If the jet cooling software is equipped for this system then it can indicate the problematic pin at the machine for the operator to take quick corrective action.
Option 2: Detecting pin breakage in critical pins
For detection pin breakage in critical pins need to use Flow sensing device (FSD). This senses water flow during the cycle and generates an alarm for any deviation. Low water flow indicates breakage or blockage or leakage of the pins.
If the jet cooling software is equipped for this system then it can indicate the problematic pin at the machine for the operator to take quick corrective action.
Recent developments
Die casters who wish to have larger control over the process manufacturing castings over 1600 tons and above have started monitoring the temperature and flow of every core pin.
This is to have better understanding, control and a stable process.
******************************************
RAGA has been one of the pioneers in jet cooling technology with over 13 years of experience serving more than 350+ die casters in over 17 countries.
For state-of-the-art cooling technology that will potentially save you huge costs in the long run email us at rahat@ragagroup.com