Reduce Shrinkage porosity rejections around core pins & thin sections? Soldering & erosion of core pins?
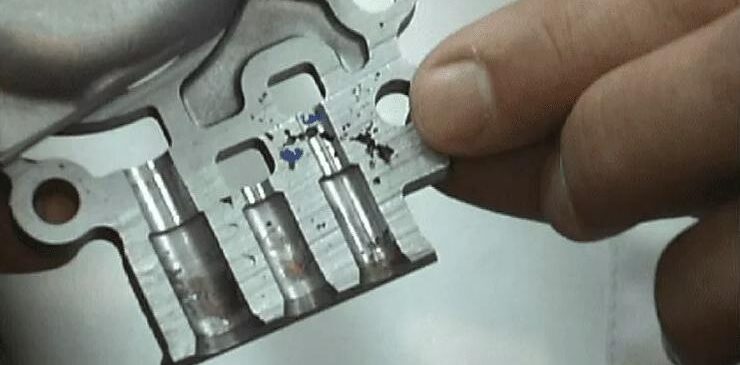
Die casting is facing acute challenges to produce defect free casting with intricate, thinner & complex profiles. With stringent requirements of porosity levels from the customers, there is an increasing need to deploy solutions to minimise them.
There are three major defects while working with core pins or around thin sections:
- Shrinkage porosity around core pins & thin sections
- Soldering on core pins
- Erosion of core pins
These defects are responsible for losses like frequent die maintenance, increased breakdown & higher casting rejections.
Shrinkage Porosity around core pins & thin sections: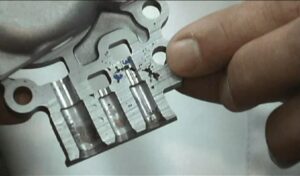
Shrinkage porosity refers to the formation of voids or cavities in a material during the solidification process. It occurs due to the uneven solidification and contraction of the molten metal, resulting in incomplete filling of the mold. Shrinkage porosity is commonly observed in areas with thin sections, complex geometries, and around core pins.
Soldering On Core Pin
Soldering refers to the adhesion of molten metal to the core pin surface. During solidification, the molten metal can flow into small gaps or recesses around the core pins, creating a metallurgical bond. Soldering not only leads to shrinkage porosity but also causes difficulties in removing the core pins after casting, potentially resulting in component damage.
Erosion of Core Pins
The Alloy temperature is around 700°C while the annealing temperature of Core Pin (H13) material is only 585°C. Continuous interaction of metal with steel leads to the gradual reduction in hardness – resulting in erosion of the core pin. Ultimately, leading to reduction of the core pin life and its quality.
Losses Due to these Defects
- Rejection of parts after machining
- Failure of casting in leak, pressure, tensile and porosities testing
- Dimensional variation in hole formed by core pins
- Assembly and functional problems
- Increased consumable spare cost
- Increased maintenance cost & machine downtime
- Resulting in less overall equipment efficiency
Cooling Solution to end these defects once and for all
Cooling the pins with optimum pressure and time control can potentially minimise all the defects. This process requires “jet cool tubes or jet coolers” to take water inside the core pins up to an optimum length which is carried in a cyclic manner.
The two-step process is as follows:
- Cooling of narrow core pins by injecting highly pressurized water which is temperature balanced.
- The second is to purge out all the water from lines and jet cool tubes so as to prevent any other defects from occurring.
Cost & time saving benefits of Jet Cooling
- Enhanced ability to cast intricate and critical parts
- Reduce or eliminate hole processing after casting
- Reduced die maintenance
- Decreased downtime of casting machines
- Increased life & reduction in cost of die parts like core pins
- Reduction in post machining & pressure leakage rejections
- Better process stability and control
- Branded as a high technology caster
Raga Group has been pioneers in Jet Cooling technology. Over 350 die casters have minimised shrinkage porosity using this machine.
If you are struggling with how to
- Implement jet cooling in your existing mold
- Implement in the new mold
Email FREE guide to rahat@ragagroup.com to get on “5 quick steps to convert your existing mold into one with Jet cooling”