Jet Cooling in Die Casting: Improving Quality and Efficiency
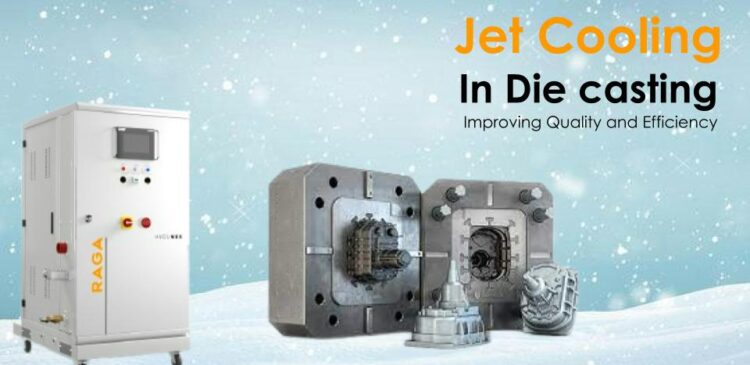
Die casting is a manufacturing process that involves injecting molten metal into a die or mold to create a part. During the process, the molten metal is cooled and solidified to create a solid part. One of the challenges in die casting is achieving a thermal balance of mold to prevent defects. Jet cooling is a technique that can help to achieve thermal balance by cooling the core pin and insert quickly and efficiently.
What is Jet Cooling?
Jet cooling is a cooling technique that uses high-pressure water to cool the core pin or insert of die casting during the solidification of casting. After water flow, pressurized air is purged to remove water droplets.
In jet cooling, a Jet cooler is used to deliver the high-pressure cold water in a core pin or an insert.
Benefits of Jet Cooling in Die Casting
Improved part quality: Jet cooling can help to reduce the formation of Die casting defects such as shrinkage porosity and soldering. By cooling the core pins and insert quickly, jet cooling can prevent the formation of these defects.
Reduced cycle time: Jet cooling can help to reduce the cycle time of the die-casting process. By cooling the die and the casting quickly, the casting can be ejected from the die more quickly, allowing for a faster cycle time and increased production efficiency.
Longer core pin and insert life: Jet cooling can help to prolong the life of the die. By cooling the core pin and insert quickly, jet cooling can help to prevent washout and other forms of damage to the die.
Energy efficiency: Jet cooling can be more energy efficient than other cooling methods. By using high-pressure water, jet cooling can cool the die and the casting more quickly and with less energy.
Challenges of Jet Cooling in Die Casting
While jet cooling offers many benefits in die casting, it also presents some challenges. For example, If the core pin break and high-pressure water mix with molten aluminum then a major accident can happen.
To address these challenges, die-casting manufacturers must carefully use a monitoring system with jet cooling lines to detect breakage of the core pin.
Conclusion
Jet cooling is a valuable technique in die casting that can improve the quality of the final product, increase production efficiency, and reduce the cost of the process. By cooling the die and the casting quickly and efficiently, jet cooling can prevent defects and maintain a fast cycle time, while also prolonging the life of the die. However, die-casting manufacturers must use a monitoring system in jet cooling lines to detect core pin breakage in the cooling line.