Die Casting Automation Systems – Revolutionizing Manufacturing
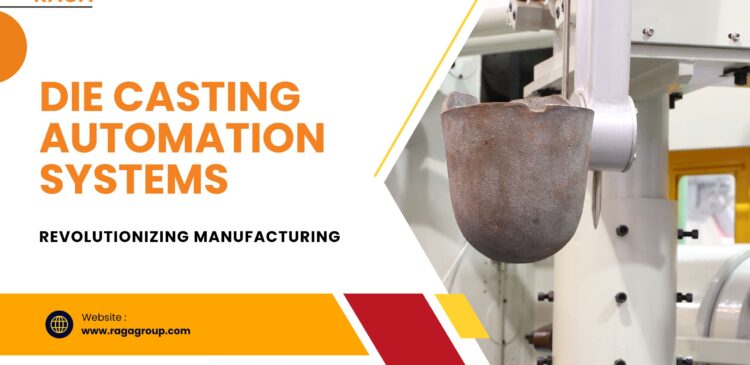
The manufacturing industry is a fast paced industry where die casting automation systems are leading a quiet revolution—delivering faster production, higher precision, and significant cost savings. As smart manufacturing gains momentum, automation in die casting has become essential for companies looking to stay competitive and efficient in a global market.
Whether you’re producing automotive parts or electronics housings, integrating automated die casting technology can unlock new levels of consistency, safety, and sustainability.
This blog will explore how die casting automation systems are reshaping modern manufacturing by enhancing production speed, reducing defects, cutting operational costs, and improving workplace safety. From robotic handling to AI-powered quality control, we’ll dive into the key components, benefits, challenges, and future innovations driving the rise of smart die casting in industries like automotive, aerospace, and electronics.
What Are Die Casting Automation Systems?
Die casting automation involves the use of robotics, sensors, and smart software to streamline the die casting process—from material handling and mold lubrication to quality inspection and part ejection. These systems reduce human intervention, boost productivity, and improve product quality across the board.
The Growing Importance of Smart Manufacturing
Smart manufacturing uses AI, IoT, and real-time data analytics to drive intelligent decision-making and automation. In die casting, this translates into minimized waste, enhanced process control, and maximized output.
Key Components of Die Casting Automation Systems
- Robotic Handling & Material Feeding Systems
Precision-controlled robots automate metal feeding, part extraction, and transport, ensuring consistent and swift handling. - Automated Mold Lubrication & Cooling
Timed lubrication and cooling processes optimize mold life and casting quality. - AI-Powered Defect Detection & Quality Control
Machine vision systems and AI algorithms detect defects like porosity and cracks early in the process. - Real-Time Data Monitoring
Integrated sensors and dashboards allow manufacturers to track cycle times, temperature, pressure, and more for instant optimization.
Benefits of Implementing Die Casting Automation
A. Improved Production Speed & Efficiency
– Automation reduces manual delays and increases cycle throughput.
– Enhanced accuracy in metal injection improves part uniformity.
B. Defect Prevention & Quality Enhancement
– Sensors detect potential issues mid-process, reducing post-production rejects.
– Automation ensures stable process parameters that minimize casting flaws like shrinkage and porosity.
C. Lower Operational Costs & Waste Reduction
– Controlled material use and fewer rejected parts reduce raw material costs.
– Automated systems optimize energy usage and minimize scrap.
D. Worker Safety & Labor Optimization
– Reduces human exposure to high-heat, high-risk environments.
– Allows skilled labor to focus on oversight, maintenance, and high-level tasks rather than repetitive work.
Challenges in Adopting Die Casting Automation Systems
While the benefits are substantial, adoption comes with hurdles:
– High Upfront Investment in automation technology and robotics.
– Integration Complexity with legacy die casting machines.
– Ongoing Maintenance and the need for regular software updates and technician training.
Innovations & Future Trends in Die Casting Automation
The future of automated die casting lies in innovation:
– AI-Driven Predictive Maintenance: Reduce downtime with systems that predict machine failures before they happen.
– IoT-Based Remote Monitoring: Manage entire casting processes from offsite with smart alerts and analytics dashboards.
– Sustainable Automation: Advanced systems that reduce energy consumption and carbon footprint while improving part quality.
Conclusion
As manufacturing enters the era of Industry 4.0, die casting automation systems are no longer optional—they’re essential. Automation not only ensures higher output and lower costs but also unlocks smarter, safer, and more sustainable production practices.
If you’re a manufacturer looking to improve efficiency and precision, now is the time to explore advanced smart die casting technologies.
Frequently Asked Questions (FAQs)
Q1: How do die casting automation systems improve efficiency?
A1: They reduce manual handling, optimize cycle times, and enhance quality control with AI-driven technology.
Q2: What are the biggest advantages of automated defect detection in die casting?
A2: Real-time detection minimizes defects, reduces rework, and improves overall product quality.
Q3: Can automation reduce manufacturing costs in die casting?
A3: Yes, by lowering labor costs, reducing material waste, and saving energy, automation significantly cuts expenses.
Q4: What industries benefit the most from die casting automation?
A4: Automotive, aerospace, electronics, and industrial machinery industries benefit greatly due to their demand for precision and volume.
Q5: What is the future of AI-driven automation in die casting?
A5: AI will power predictive maintenance, quality control, and energy efficiency, driving smarter and more adaptive casting systems.