Understanding Aluminum Die Casting Parts: Benefits, Applications, and Insights
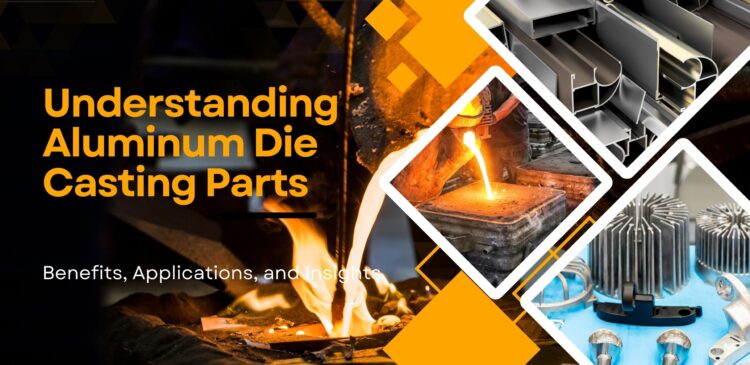
In the world of manufacturing, aluminum die-casting parts are important components that power industries from automotive to aerospace. But what makes these parts so essential? Why is aluminum the preferred material for die casting processes across the globe?
This blog will explore the aluminum die casting process, the benefits it offers, and the industries that depend on these durable components.
What Are Aluminum Die Casting Parts?
Aluminum die-casting parts are precision-engineered metal components formed by injecting molten aluminum into a mould cavity under high pressure. Once cooled and solidified, the result is a high-strength, lightweight product used across a variety of applications.
Why Is Aluminum Ideal for Die Casting?
Aluminum is favoured in die casting due to its:
– High strength-to-weight ratio
– Corrosion resistance
– Excellent thermal and electrical conductivity
– Cost-effectiveness for mass production
– Recyclability, supporting sustainability goals
Industries That Rely on Aluminum Die Casting Components
Aluminum casting components are used widely in:
– Automotive: Engine blocks, gearboxes, wheels, transmission housings
– Aerospace: Lightweight structural components, engine parts
– Electronics: Housings, heat sinks, casings
– Industrial Machinery: Gears, brackets, enclosures, and frames
These industries rely on the durability and precision that only aluminum die casting can deliver.
How Aluminum Die Casting Works?
The aluminum casting process typically involves:
- Mould preparation – Moulds (dies) are made from high-grade steel.
- Injection – Molten aluminum is injected under high pressure into the mould cavity.
- Cooling – The aluminum cools rapidly and solidifies.
- Ejection & Trimming – The part is ejected and trimmed to meet exact specifications.
High-Pressure vs. Low-Pressure Die Casting.
- High-pressure die casting: Faster, better for high-volume production
- Low-pressure die casting: Slower, used for thicker walls and larger parts with higher strength requirements.
Common Aluminum Die Casting Parts & Their Uses.
1. Automotive
– Engine blocks and gearbox housings for weight reduction and fuel efficiency
– Alloy wheels that combine style with durability
2. Aerospace
– Lightweight components that reduce overall aircraft weight without sacrificing strength.
3. Electronics
– Heat-dissipating casings to protect delicate circuitry
4. Industrial Applications
– Structural components in heavy machinery
– Mechanical parts exposed to high wear
Benefits of Aluminum Die Casting Parts
✔ Lightweight but Strong
✔ Excellent Corrosion Resistance
✔ Fast & Cost-Efficient Production
✔ Superior Heat Dissipation
✔ Design Flexibility for Complex Shapes
✔ Sustainable & Recyclable
With aluminum die casting, manufacturers can achieve tight tolerances, sharp detail, and repeatable consistency across thousands of units.
Challenges & Solutions in Aluminum Die Casting
Despite its many advantages, aluminum die casting has some technical challenges:
1. Porosity Issues
Air bubbles during casting can cause weak points. Vacuum die casting and proper venting design can reduce this risk.
2. Precision Mould Design
Incorrect mould flow paths can lead to defects. Using simulation software and thermal analysis helps optimize the design.
3. Quality Control
Implementing real-time monitoring systems and non-destructive testing (NDT) ensures consistent quality in every batch.
Conclusion
Aluminum die casting parts offer a unique blend of strength, lightness, and design versatility that makes them indispensable in modern manufacturing. From your car’s engine to aerospace components, these parts are the unsung heroes of industrial innovation.
As industries move towards more efficient and sustainable production methods, aluminum die casting continues to stand out as the go-to solution for quality, performance, and scalability.
Frequently Asked Questions (FAQ’s)
Q1: What are the main advantages of aluminum die casting parts?
A1: They are lightweight, durable, corrosion-resistant, and cost-effective. Ideal for high-volume and precision applications.
Q2: Which industries use aluminum casting components the most?
A2: Automotive, aerospace, electronics, and industrial manufacturing industries rely heavily on aluminum casting.
Q3: How does aluminum die casting differ from other casting methods?
A3: It uses high-pressure injection, enabling faster production, tighter tolerances, and smoother finishes compared to sand casting.
Q4: What are the common defects in aluminum die casting and their solutions?
A4: Porosity and shrinkage can be reduced with vacuum casting and optimized mould design. Real-time monitoring helps as well.
Q5: Why is aluminum preferred in die casting?
A5: Due to its high strength, lightness, corrosion resistance, and ability to dissipate heat effectively.