Understanding and Preventing Porosity Defects in Casting
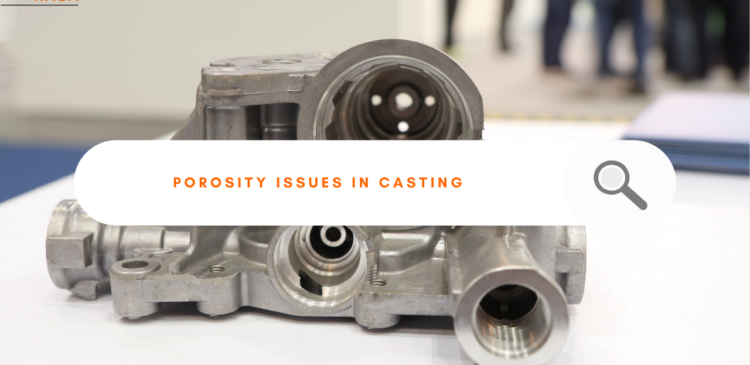
Did you know that porosity defects are responsible for up to 60% of quality issues in metal casting? These tiny voids can compromise the strength and functionality of critical components, leading to costly failures.
Porosity defects in casting are a common challenge in manufacturing, impacting the structural integrity and appearance of cast products. This blog explores the causes, effects, and prevention methods to ensure high-quality castings.
What is Porosity in Casting?
Definition
Porosity in casting refers to tiny holes or voids within the material, which occur during the solidification process. These defects can appear as surface pits or internal cavities.
Types of Porosity
- Gas Porosity: Caused by trapped gases within the molten metal.
- Shrinkage Porosity: Results from the contraction of metal as it cools and solidifies.
Causes of Porosity Defects in Casting
Gas Porosity
- Trapped gases due to improper venting.
- Contaminated or wet materials.
- Rapid cooling, which prevents gases from escaping.
Shrinkage Porosity
- Inadequate feeding of molten metal.
- Poor mold design restricting metal flow.
- Uneven or rapid cooling rates.
Identifying Porosity in Castings
Inspection Methods
- X-ray Inspection: Detects internal voids and gas pockets.
- Ultrasonic Testing: Uses sound waves to identify inconsistencies within the casting.
Visual Indicators
- Surface pits and irregularities.
- Visible internal voids after machining or sectioning.
Effects of Porosity Defects on Casting Quality
Mechanical Properties:
- Reduced strength and durability.
- Increased risk of fractures or failures under load.
Aesthetic Impact:
- Surface blemishes affecting the product’s appearance.
- Poor finish, which may require additional processing.
Preventing Porosity Defects in Casting
Proper Mold Design:
- Ensure adequate venting to release trapped gases.
- Optimize risers and feeders to improve molten metal flow.
Degassing Techniques:
- Use argon or nitrogen to remove gases from molten metal.
- Employ vacuum degassing for critical applications.
Controlled Cooling:
- Implement gradual cooling to reduce stress and prevent shrinkage voids.
Examples
Aluminum Casting:
- Example: Automotive engine blocks often experience gas porosity.
- Solution: Improved degassing and controlled cooling reduced defects by 40%.
Gold Casting:
- Example: Jewelry casting often suffers from shrinkage porosity.
- Solution: Precision mold design and temperature control minimized defects, enhancing quality.
Future Trends and Innovations
Advanced Materials:
- Development of nano-engineered alloys to resist porosity.
Technological Advancements:
- Use of advanced techniques like nano drilling to create precision molds.
- Automated inspection systems for early defect detection.
Sustainability:
- Adoption of eco-friendly practices in casting to reduce waste and improve quality.
Conclusion
Porosity defects in casting can significantly impact product quality, but understanding their causes and implementing preventive measures can mitigate these issues. By leveraging advanced materials, innovative technologies, and sustainable practices, manufacturers can produce defect-free castings that meet the highest standards. Ensure your castings are defect-free by implementing these best practices and partnering with reputable suppliers equipped with the latest technologies.
FAQs
Q: What are porosity defects in casting, and why are they significant?
A: Porosity defects are voids or holes within cast materials, affecting their strength and quality. Addressing these defects is crucial for ensuring the durability and performance of cast products.
Q: What causes gas porosity defects in casting, and how can they be prevented?
A: Gas porosity arises from trapped gases due to improper venting or rapid cooling. Prevent it by degassing molten metal, ensuring clean materials, and optimizing cooling rates.
Q: What is shrinkage porosity, and what factors contribute to it?
A: Shrinkage porosity occurs when metal contracts during solidification. Factors include inadequate feeding, poor mold design, and rapid cooling. Prevention involves proper riser design and controlled cooling.
Q: How can porosity defects in castings be identified and inspected?
A: Use X-ray and ultrasonic testing for internal voids, and visual inspection for surface irregularities.
Q: What are the common types of porosity defects found in aluminum castings, and how can they be addressed?
A: Gas and shrinkage porosity are common in aluminum castings. Degassing and optimized mold designs can address these issues effectively.
Q: How does porosity affect the quality and appearance of gold castings, and what can be done to minimize it?
A: Porosity weakens structural integrity and causes blemishes in gold castings. Minimize it with high-quality alloys, precision molds, and controlled casting conditions.
Q: What future trends and innovations are emerging in the prevention of porosity defects in casting?
A: Emerging trends include advanced materials, nano drilling, and sustainable practices to reduce defects and enhance overall quality.